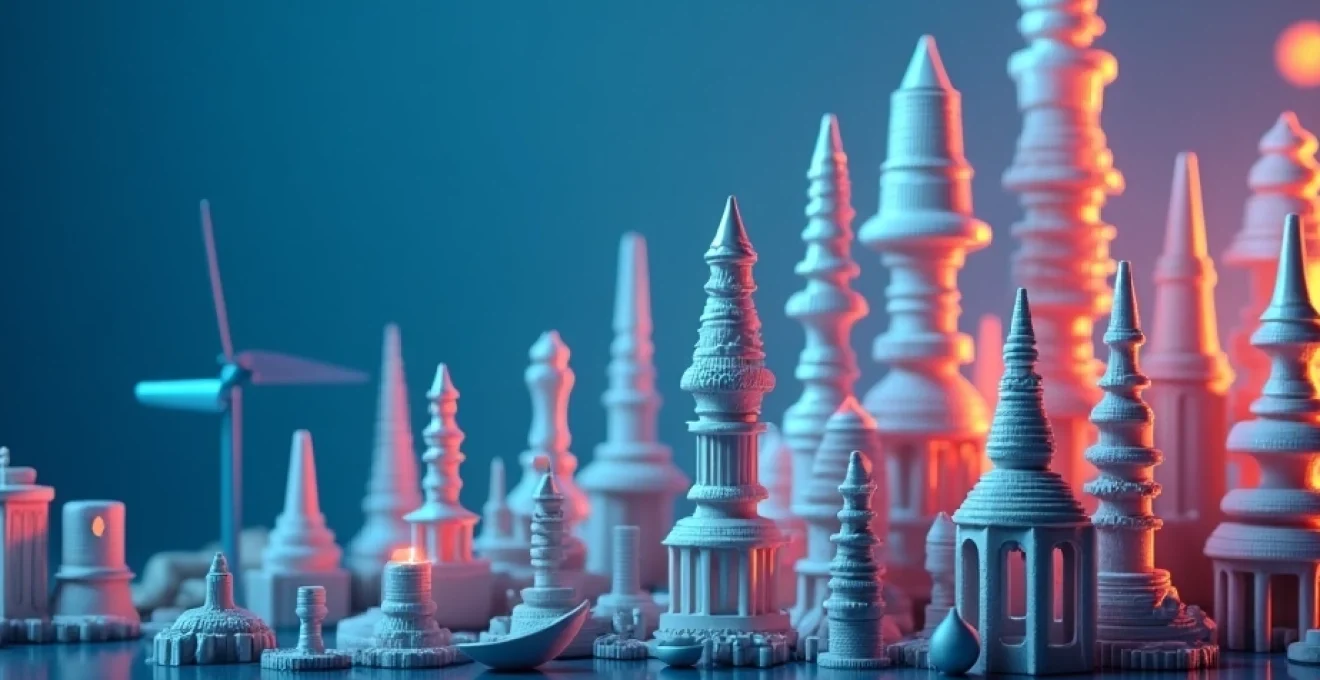
L'impression 3D révolutionne les processus de fabrication et ouvre de nouvelles perspectives pour l'innovation industrielle. Cette technologie de fabrication additive permet de créer des objets tridimensionnels en déposant des matériaux couche par couche, offrant une liberté de conception sans précédent. Des secteurs aussi variés que l'aérospatiale, la médecine ou l'automobile exploitent désormais le potentiel de l'impression 3D pour développer des produits innovants, optimiser leurs processus et réduire leurs coûts. Examinons en détail comment cette technologie transforme l'industrie et façonne l'avenir de la production.
Technologies d'impression 3D pour l'innovation industrielle
L'impression 3D regroupe plusieurs technologies distinctes, chacune avec ses avantages spécifiques. Le choix de la technique dépend des exigences en termes de matériaux, de précision et d'applications visées. Voici un aperçu des principales technologies d'impression 3D utilisées dans l'industrie :
Stéréolithographie (SLA) et sa précision micronique
La stéréolithographie est l'une des technologies d'impression 3D les plus anciennes et les plus précises. Elle utilise un laser pour polymériser une résine photosensible couche par couche. La SLA permet d'obtenir des pièces avec une finition de surface exceptionnelle et une précision de l'ordre du micron. Cette technologie est particulièrement adaptée pour réaliser des prototypes esthétiques, des moules pour le moulage par injection ou des guides chirurgicaux sur mesure en médecine.
La précision micronique de la SLA en fait un choix privilégié pour les applications nécessitant un haut niveau de détail, comme la joaillerie ou la dentisterie. Par exemple, les prothèses dentaires imprimées en 3D par SLA offrent un ajustement parfait grâce à cette résolution exceptionnelle. La SLA permet également de produire rapidement des masters pour la fabrication de moules en silicone utilisés dans la production de petites séries.
Frittage sélectif par laser (SLS) pour prototypes fonctionnels
Le frittage sélectif par laser (SLS) utilise un laser puissant pour fritter des poudres polymères et créer des objets solides. Cette technologie présente l'avantage de pouvoir produire des pièces fonctionnelles sans structures de support, offrant une grande liberté de conception. Le SLS est particulièrement adapté pour réaliser des prototypes fonctionnels, des pièces mécaniques complexes ou des composants pour l'industrie aérospatiale.
L'un des atouts majeurs du SLS est sa capacité à produire des pièces avec des propriétés mécaniques proches de celles obtenues par injection plastique. Cela en fait une solution idéale pour le prototypage rapide et la production de petites séries. Par exemple, l'industrie automobile utilise le SLS pour tester rapidement de nouveaux designs de pièces avant de lancer la production en série.
Dépôt de fil fondu (FDM) et son accessibilité pour les PME
Le dépôt de fil fondu (FDM) est la technologie d'impression 3D la plus répandue et la plus accessible. Elle consiste à extruder un filament thermoplastique fondu pour construire l'objet couche par couche. Bien que moins précise que la SLA ou le SLS, la FDM offre un excellent rapport coût-efficacité, ce qui la rend particulièrement attractive pour les PME souhaitant intégrer l'impression 3D dans leurs processus.
La simplicité et le faible coût des imprimantes FDM en font un choix populaire pour le prototypage rapide et la fabrication de pièces fonctionnelles non critiques. De nombreuses startups utilisent cette technologie pour valider leurs concepts de produits avant d'investir dans des méthodes de production plus coûteuses. La FDM est également très utilisée dans l'éducation pour initier les étudiants à la conception et à la fabrication additive.
Fusion par faisceau d'électrons (EBM) dans l'aérospatiale
La fusion par faisceau d'électrons (EBM) est une technologie d'impression 3D métallique haut de gamme. Elle utilise un faisceau d'électrons pour faire fondre une poudre métallique et créer des pièces de haute densité. L'EBM est particulièrement appréciée dans l'industrie aérospatiale pour sa capacité à produire des composants en titane légers et résistants.
L'un des principaux avantages de l'EBM est la qualité métallurgique des pièces produites, qui peuvent atteindre des propriétés mécaniques comparables à celles des pièces forgées. Cette technologie permet de fabriquer des composants aéronautiques complexes en une seule pièce, réduisant ainsi le nombre d'assemblages et améliorant la fiabilité. Par exemple, des fabricants de moteurs d'avion utilisent l'EBM pour produire des aubes de turbine optimisées et plus légères.
Matériaux innovants en impression 3D
L'évolution rapide des technologies d'impression 3D s'accompagne du développement de nouveaux matériaux aux propriétés uniques. Ces matériaux innovants ouvrent la voie à des applications jusqu'alors impossibles avec les méthodes de fabrication traditionnelles. Explorons quelques-uns des matériaux les plus prometteurs utilisés en impression 3D :
Alliages de titane pour implants médicaux personnalisés
Les alliages de titane imprimés en 3D révolutionnent le domaine des implants médicaux personnalisés. Grâce à leur biocompatibilité et leurs excellentes propriétés mécaniques, ces alliages permettent de créer des prothèses et des implants parfaitement adaptés à l'anatomie de chaque patient. L'impression 3D offre la possibilité de concevoir des structures poreuses qui favorisent l'ostéointégration, améliorant ainsi la durabilité et le confort des implants.
Un exemple marquant est l'utilisation d'implants crâniens en titane imprimés en 3D pour la reconstruction maxillo-faciale. Ces implants sur mesure offrent une précision incomparable et réduisent considérablement le temps d'intervention chirurgicale. De plus, la liberté de conception permise par l'impression 3D permet d'optimiser la répartition des contraintes mécaniques, prolongeant ainsi la durée de vie des implants.
Polymères à mémoire de forme dans l'automobile
Les polymères à mémoire de forme imprimés en 3D trouvent des applications innovantes dans l'industrie automobile. Ces matériaux ont la capacité de changer de forme en réponse à des stimuli externes comme la température ou le courant électrique. Cette propriété unique ouvre la voie à des composants automobiles adaptatifs et intelligents.
Par exemple, des constructeurs automobiles expérimentent l'utilisation de grilles de radiateur imprimées en 3D avec des polymères à mémoire de forme. Ces grilles peuvent s'ouvrir ou se fermer automatiquement en fonction de la température du moteur, optimisant ainsi l'aérodynamisme et la consommation de carburant. D'autres applications potentielles incluent des systèmes de déploiement d'airbags plus efficaces ou des panneaux de carrosserie auto-réparables.
Biomatériaux imprimables pour l'ingénierie tissulaire
L'impression 3D de biomatériaux représente une avancée majeure pour l'ingénierie tissulaire et la médecine régénérative. Ces matériaux biocompatibles et biodégradables peuvent être chargés de cellules vivantes pour créer des structures tissulaires complexes. Les chercheurs explorent activement le potentiel de ces biomatériaux pour la fabrication d'organes artificiels et la réparation de tissus endommagés.
Un domaine particulièrement prometteur est l'impression 3D de scaffolds (échafaudages) pour la régénération osseuse. Ces structures poreuses imprimées en 3D à partir de biomatériaux comme le polycaprolactone (PCL) ou l'hydroxyapatite servent de support à la croissance cellulaire et favorisent la formation de nouveau tissu osseux. Cette approche pourrait révolutionner le traitement des fractures complexes et des grandes pertes osseuses.
Composites carbone-PEEK pour pièces haute performance
Les composites carbone-PEEK (polyétheréthercétone) imprimés en 3D gagnent en popularité pour la fabrication de pièces haute performance. Ce matériau allie la légèreté et la résistance des fibres de carbone aux excellentes propriétés mécaniques et thermiques du PEEK. L'impression 3D permet de créer des structures complexes optimisées pour maximiser les performances tout en minimisant le poids.
L'industrie aérospatiale est l'un des principaux utilisateurs de ces composites avancés. Des fabricants d'avions utilisent l'impression 3D carbone-PEEK pour produire des composants de moteur légers et résistants aux hautes températures. Dans le domaine médical, ce matériau trouve des applications dans la fabrication d'implants orthopédiques durables et biocompatibles. La liberté de conception offerte par l'impression 3D permet d'optimiser la distribution des fibres de carbone pour obtenir les propriétés mécaniques souhaitées.
Applications révolutionnaires de l'impression 3D
L'impression 3D transforme radicalement de nombreux secteurs industriels, offrant des solutions innovantes à des problèmes complexes. Voici quelques exemples d'applications révolutionnaires qui illustrent le potentiel disruptif de cette technologie :
- Aérospatiale : Fabrication de composants de moteur optimisés et allégés
- Médecine : Impression d'implants et de prothèses sur mesure
- Automobile : Prototypage rapide et production de pièces personnalisées
- Architecture : Création de maquettes complexes et impression de structures à grande échelle
- Mode : Conception de vêtements et d'accessoires aux formes impossibles à réaliser traditionnellement
Dans le domaine médical, l'impression 3D permet de créer des modèles anatomiques précis pour la planification chirurgicale. Les chirurgiens peuvent s'entraîner sur des répliques exactes des organes de leurs patients avant l'intervention, réduisant ainsi les risques et améliorant les résultats. Cette approche est particulièrement utile pour les opérations complexes comme les séparations de jumeaux siamois.
L'industrie aérospatiale utilise l'impression 3D pour fabriquer des pièces de satellites aux géométries complexes. Ces composants optimisés permettent de réduire le poids des satellites tout en améliorant leurs performances. Par exemple, des supports d'antenne imprimés en 3D peuvent intégrer des canaux de refroidissement internes impossibles à réaliser avec les méthodes de fabrication traditionnelles.
Dans le secteur de la construction, des entreprises expérimentent l'impression 3D de bâtiments entiers. Cette approche permet de réduire considérablement les délais et les coûts de construction, tout en offrant une grande liberté architecturale. Des projets pilotes d'habitations imprimées en 3D ont déjà vu le jour dans plusieurs pays, ouvrant la voie à une révolution dans le secteur du logement abordable.
Défis techniques et solutions en impression 3D
Malgré ses nombreux avantages, l'impression 3D fait face à plusieurs défis techniques qui limitent encore son adoption à grande échelle dans certains secteurs. Heureusement, les chercheurs et les industriels travaillent activement au développement de solutions innovantes pour surmonter ces obstacles. Examinons quelques-uns des principaux défis et les approches prometteuses pour les résoudre :
Optimisation topologique pour réduction de poids
L'optimisation topologique est une technique de conception assistée par ordinateur qui vise à créer des structures légères et résistantes en optimisant la distribution de matière. Cette approche est particulièrement bien adaptée à l'impression 3D, qui permet de fabriquer des géométries complexes impossibles à réaliser avec les méthodes traditionnelles.
Les algorithmes d'optimisation topologique analysent les contraintes mécaniques subies par une pièce et génèrent automatiquement une structure optimisée qui maximise la résistance tout en minimisant le poids. Cette technique est largement utilisée dans l'aérospatiale et l'automobile pour créer des composants allégés sans compromettre leurs performances. Par exemple, des supports de moteur d'avion optimisés topologiquement et imprimés en 3D peuvent être jusqu'à 40% plus légers que leurs équivalents usinés traditionnellement.
Gestion des contraintes résiduelles post-impression
Les contraintes résiduelles sont un défi majeur en impression 3D métallique. Ces contraintes internes, générées par les cycles thermiques rapides lors du processus d'impression, peuvent entraîner des déformations ou des fissures dans les pièces finales. La gestion de ces contraintes est cruciale pour garantir la qualité et la fiabilité des composants imprimés en 3D.
Plusieurs approches sont explorées pour minimiser les contraintes résiduelles. L'une d'elles consiste à optimiser les paramètres d'impression, comme la puissance du laser et la stratégie de balayage, pour réduire les gradients thermiques. Une autre solution prometteuse est l'utilisation de systèmes de préchauffage du lit de poudre, qui permettent de réduire les différences de température et donc les contraintes induites. Des traitements thermiques post-impression sont également couramment utilisés pour relaxer les contraintes résiduelles.
Contrôle qualité in-situ par imagerie thermique
Le contrôle qualité est un enjeu crucial pour l'adoption de l'impression 3D dans des secteurs exigeants comme l'aérospatiale ou le médical. Les systèmes de contrôle in-situ par imagerie thermique représentent une avancée majeure dans ce domaine. Ces systèmes utilisent des caméras infrarouges pour surveiller en temps réel la température du bain de fusion lors de l'impression.
L'analyse des données thermiques permet de détecter rapidement d'éventuelles anomalies, comme des zones de surchauffe ou des manques de fusion, qui pourraient compromettre la qualité de la pièce. Cette approche permet non seulement
L'analyse des données thermiques permet de détecter rapidement d'éventuelles anomalies, comme des zones de surchauffe ou des manques de fusion, qui pourraient compromettre la qualité de la pièce. Cette approche permet non seulement d'améliorer la qualité finale des pièces imprimées, mais aussi d'optimiser les paramètres d'impression en temps réel pour compenser les variations. Certains systèmes avancés peuvent même interrompre automatiquement l'impression en cas de défaut critique, évitant ainsi le gaspillage de matière et de temps.
Algorithmes de tranchage adaptatif pour structures complexes
Le tranchage, qui consiste à découper le modèle 3D en fines couches pour l'impression, est une étape cruciale du processus. Pour les structures complexes, les algorithmes de tranchage traditionnels peuvent produire des résultats sous-optimaux, compromettant la qualité et la précision de la pièce finale. Les algorithmes de tranchage adaptatif représentent une avancée significative dans ce domaine.
Ces algorithmes intelligents analysent la géométrie de la pièce et ajustent dynamiquement l'épaisseur des couches en fonction des caractéristiques locales. Par exemple, ils peuvent réduire l'épaisseur des couches dans les zones présentant des détails fins ou des surfaces courbes, tout en utilisant des couches plus épaisses pour les sections massives. Cette approche permet d'optimiser à la fois la qualité de surface et le temps d'impression. De plus, certains algorithmes avancés peuvent générer des trajectoires d'impression non planaires, suivant les contours naturels de la pièce pour améliorer ses propriétés mécaniques.
Perspectives futures de l'impression 3D
L'impression 3D continue d'évoluer à un rythme rapide, ouvrant de nouvelles perspectives fascinantes pour l'avenir de la fabrication. Explorons quelques-unes des tendances les plus prometteuses qui façonneront le futur de cette technologie révolutionnaire :
Bio-impression 4D pour organes fonctionnels
La bio-impression 4D représente la prochaine frontière dans le domaine de l'ingénierie tissulaire. Cette technologie combine l'impression 3D de biomatériaux avec des matériaux intelligents capables de changer de forme ou de fonction au fil du temps. L'objectif ultime est de créer des organes fonctionnels pour la transplantation, résolvant ainsi la pénurie chronique d'organes donneurs.
Les chercheurs travaillent sur des bioencres avancées contenant des cellules souches et des matériaux stimuli-répondants. Une fois imprimées, ces structures peuvent se développer et s'auto-organiser pour former des tissus complexes. Par exemple, des vaisseaux sanguins imprimés en 4D pourraient s'adapter à leur environnement, se ramifier et former un réseau vasculaire fonctionnel. Bien que nous soyons encore loin de pouvoir imprimer des organes entièrement fonctionnels, les progrès dans ce domaine sont rapides et prometteurs.
Fabrication additive in-situ pour exploration spatiale
L'impression 3D jouera un rôle crucial dans l'exploration spatiale future, notamment pour les missions de longue durée sur la Lune ou Mars. La fabrication additive in-situ, utilisant des matériaux disponibles sur place, permettra aux astronautes de produire des pièces de rechange, des outils et même des habitats directement sur d'autres planètes.
Des agences spatiales comme la NASA travaillent déjà sur des technologies d'impression 3D adaptées à l'environnement spatial. Par exemple, des projets de recherche visent à utiliser le régolithe lunaire ou martien comme matériau d'impression pour construire des structures. Cette approche réduirait considérablement la quantité de matériel à transporter depuis la Terre, rendant les missions spatiales plus économiques et durables. À terme, l'impression 3D pourrait même permettre la construction de colonies entières sur d'autres planètes.
Micro-impression 3D pour dispositifs microfluidiques
La micro-impression 3D repousse les limites de la miniaturisation, permettant la fabrication de structures à l'échelle micrométrique. Cette technologie trouve des applications particulièrement prometteuses dans le domaine des dispositifs microfluidiques, utilisés pour l'analyse chimique et biologique à petite échelle.
Grâce à la micro-impression 3D, il est possible de créer des labs-on-a-chip complexes intégrant des canaux, des chambres et des valves microscopiques. Ces dispositifs permettent de réaliser des analyses rapides et précises avec des volumes d'échantillons minimes, ouvrant la voie à des diagnostics médicaux plus rapides et moins coûteux. La liberté de conception offerte par l'impression 3D permet également d'optimiser les géométries des canaux pour améliorer l'efficacité des réactions chimiques ou la séparation des particules.
Intelligence artificielle dans la conception générative
L'intégration de l'intelligence artificielle (IA) dans le processus de conception pour l'impression 3D promet de révolutionner la manière dont nous créons et optimisons les objets. La conception générative assistée par IA peut explorer des millions de variations possibles pour trouver la solution optimale répondant à des critères spécifiques de performance, de poids et de coût.
Ces algorithmes avancés peuvent générer des structures organiques complexes impossibles à concevoir manuellement, maximisant les performances tout en minimisant l'utilisation de matière. Par exemple, dans l'industrie automobile, l'IA peut être utilisée pour concevoir des supports de moteur ultralégers mais extrêmement résistants, en s'inspirant des structures trouvées dans la nature. À mesure que ces outils de conception générative deviennent plus accessibles, nous pouvons nous attendre à voir émerger une nouvelle esthétique dans le design industriel, caractérisée par des formes complexes et organiques parfaitement adaptées à leur fonction.